Professional Projects


























LEKA
Leka is a locally manufactured restaurant in the Poblenou 22@ district of Barcelona, developed and manufactured at Fablab Barcelona in collaboration with a local network of distributors and trades. The restaurant is conceived as an open source platform, where all the knowledge involved, and which gives it character, is shared. In this way, all the designs, recipes, and nutritional advice are downloadable from the website.
The project is organized into several families: furniture, acoustic elements, interactive elements, etc. Each of them requires a different construction system. The furniture must be sturdy, prepared for constant movement, the ceiling light, with a geometry that breaks up the sound, the paneling with perforations, etc. For its development, we create a programmed design for each family; obtaining exportable and original systems.
This design is based on developing the common elements in each family. In this way, the furniture shares the same construction system, in turn the different triangles of the roof and so on.
Thanks to access to digital production tools, we can afford the entire prototyping process required for the production of non-standard systems. The design is developed on the basis of prototypes, 1:1 scale models, in which the principles of design, structure or manufacturing process are continuously related. Prototyping allows us to evolve the design based on its manufacturing result, evolve the programming and evolve the details until the system is ready for production. In this way, we replace plans, construction details, models with a series of full-scale prototypes. These non-standard designs are part of the Leka web platform. They can be downloaded and used to manufacture or incorporate them into other projects.
- Architects: IAAC FAB Lab Barcelona ; IAAC FAB Lab Barcelona
- Area: 100 m²
- Year: 2015
- Photographs: Javier Callejas
- Suppliers: Neopixel , ROCKWOOL , WISA
- Furniture Design: Miguel Guerrero, Ingi Guðjónsson
- City: Barcelona, Spain
ADIDAS NEMEZIZ
For the launch of the new Adidas Nemeziz boots, we helped our friends over at Espadaysantacruz to design and create the 3D model for a parametric sculpture that captures one of Messi’s most iconic plays: his goal against Bayern München in the 2014-2015 Champions League.
Developing the blueprints to build Messi’s run required both work from an animator and from parametric designers. Once the play was decided upon, videos from its broadcast were used to recreate a 3D animation that spanned from the moment he received the ball until he shot it. Each frame of the video was translated as a position in the model. After the play was reconstructed, regions of interest in the body were selected to create an array of points in space that defined the surface Messi created while running. From this representation, and through conversation with the building team, a series of slits were parametrically extracted and modified, using algorithms and also manually, to get the final shape. The main constraints were set by the construction phase, and were related to how the bands would cover the geometry and how and where the piece was to channel its weight.
The project was a digital endeavour that was then carefully prepared for the reality of a workshop.
- Client: Adidas Europe
- Agency: Iris Worldwide
- Production company: 1st Avenue Machine London
- 3d Model: Hamil Industries
- Fabrication: We Made London
- Concept, direction and design: Espadaysantacruz Studio
- June -2019












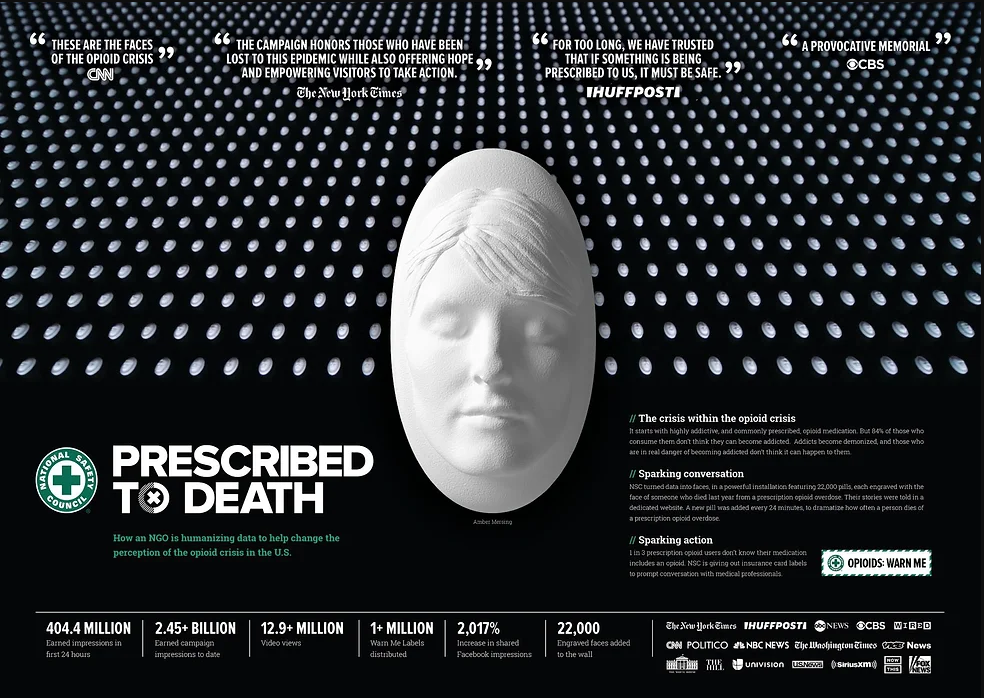
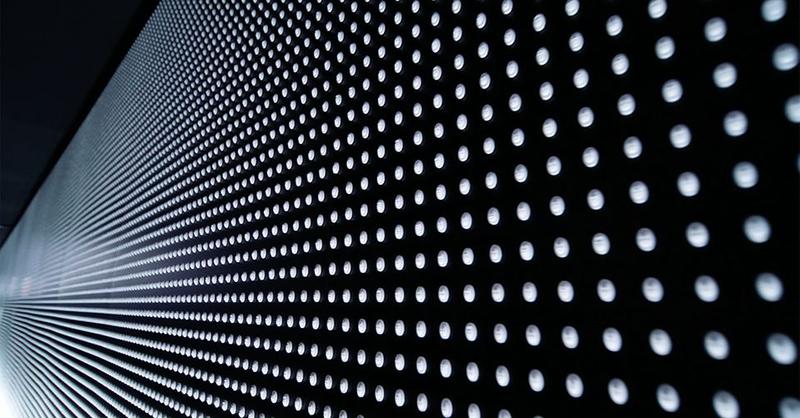
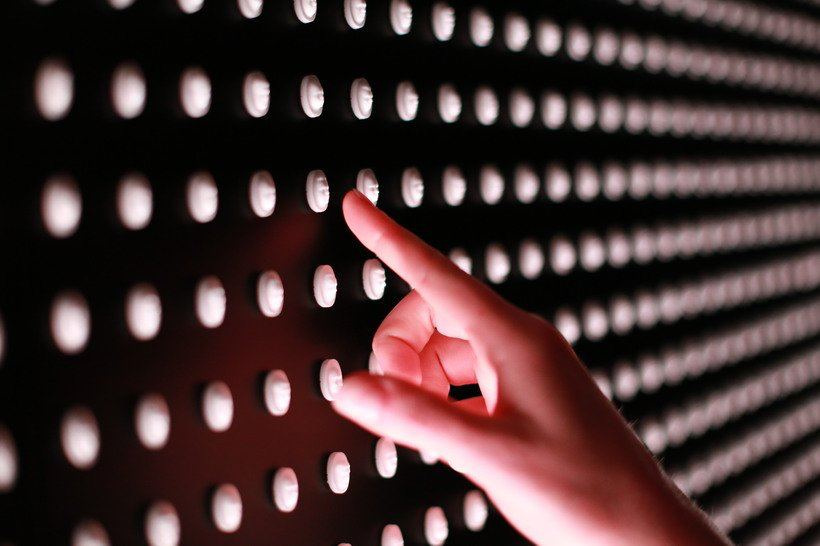
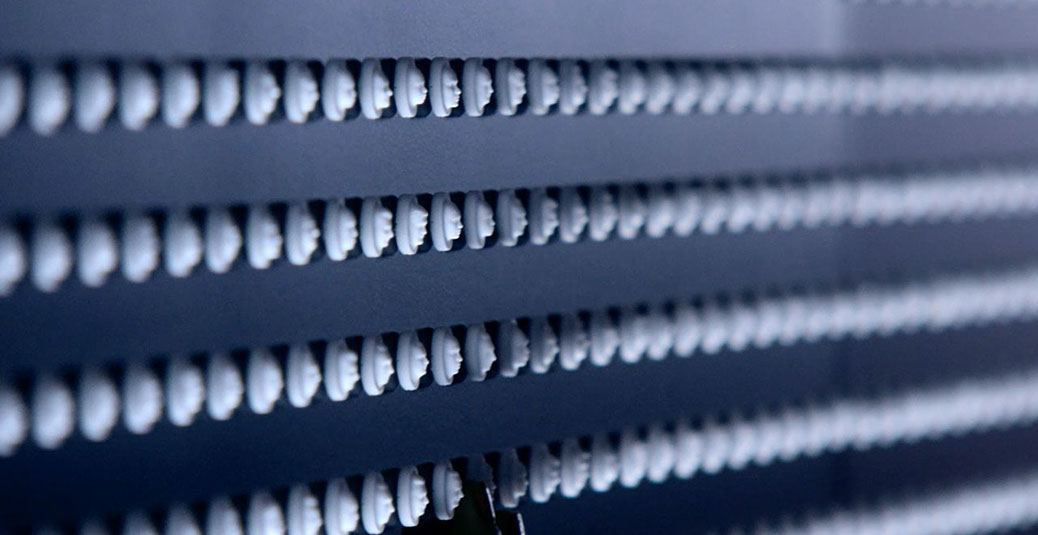
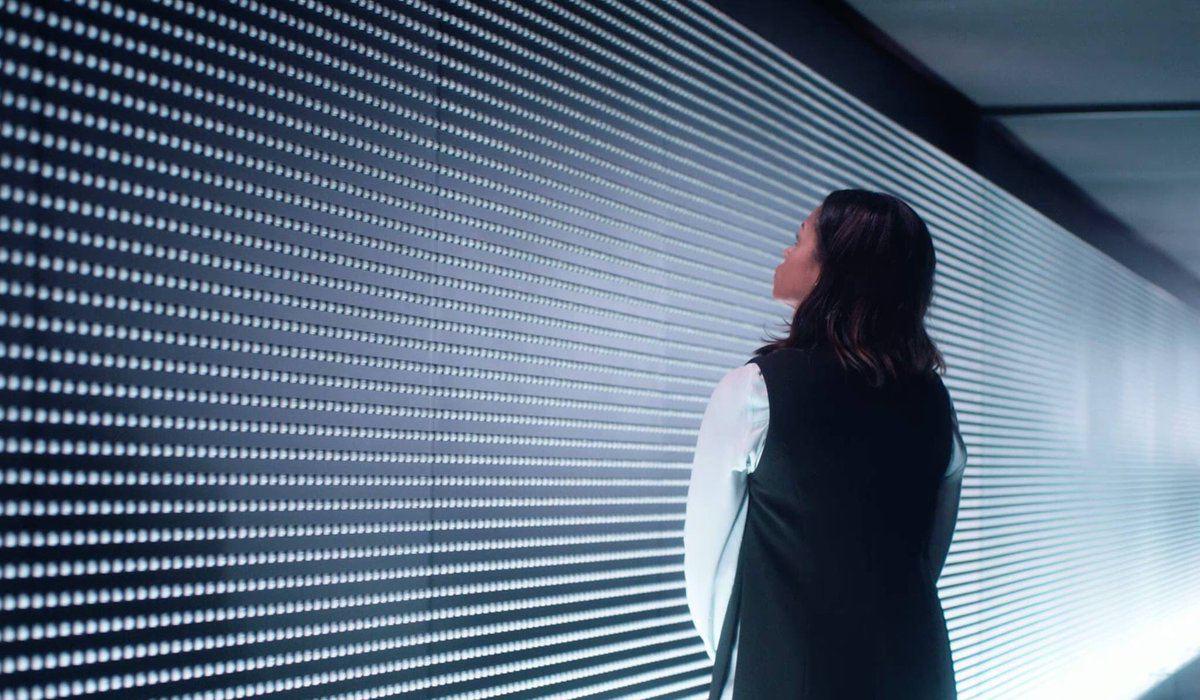
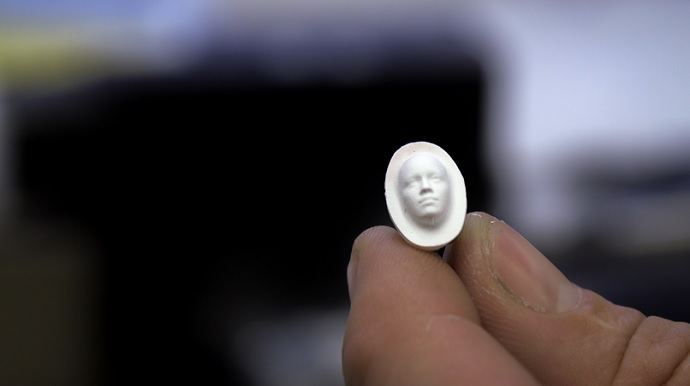

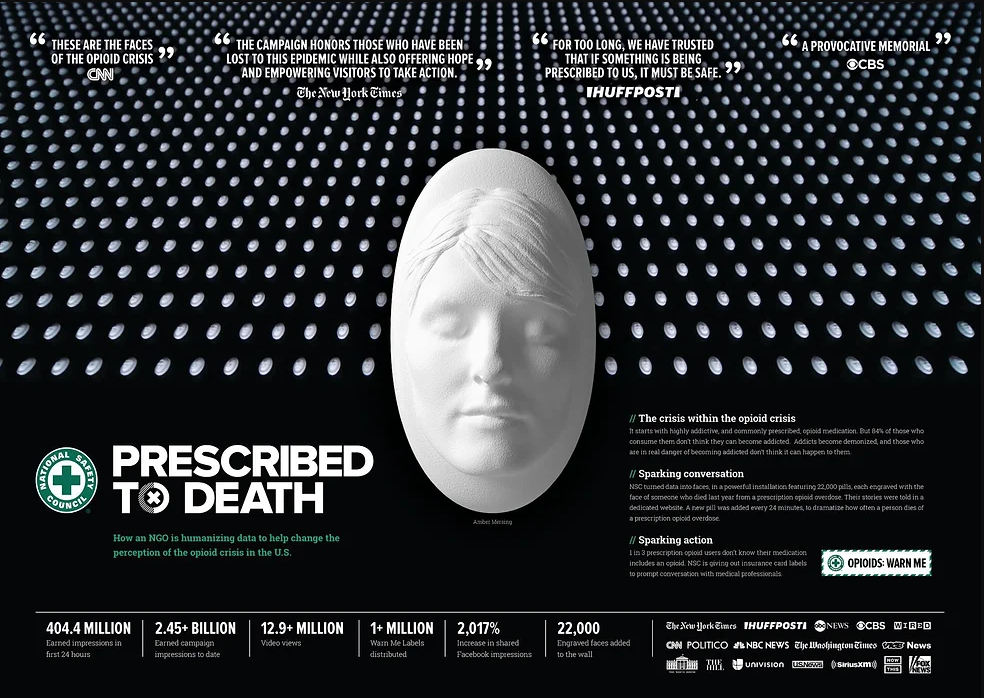
Everyday Painkillers
These are the faces of the prescription opioid crisis. Explore the memorial. Take action.
“Stop Everyday Killers” is a public education campaign that debuted in Chicago with “Prescribed to Death,” an installation featuring thousands of pills carved with human faces. The pills represent the 22,000 people who died from opioid addiction last year, as well as the lives we continue to lose. Every 24 minutes, the memorial carves an additional pill, representing the frequency with which victims succumb to their addiction.
Digital Impact
Over 11 million video views
2,017% increase in shared Facebook impressions
404,4000+ earned impressions in the first 24 hours
1,008,415,240 earned impressions overall
104,000+ Warn Me Labels distributed
2019 – Silver Lion Effectiveness, 2018 – Gold Lion Outdoor – Special Builds, 2018 – Gold Lion Outdoor – Displays, 2018 – Gold Health Lion Use Of Data, 2018 – Silver Lion Creative Data, 2018 – Bronze Lion PR – Use Of Events And Stunts , 2018 – Bronze Lion PR – Public Affairs, FWA of the Month
Press
︎︎︎ The White House, Creativity, AdWeek, Shots, The Inspiration Room
- Client: National Security Council
- Agency: Enerygy BBDO
- Production company: Mssng Peces
- Director: Tucker Walsh
- Exhibition & Experience Design:Hyphen-Labs
- Fabrication: Shane Roberts, RMI
- Creative Technologist: Rodrigo Aguirre